- Home /
- Case Studies /
- Redwood Manufacturing
Case Study: Optimizing Production Efficiency at Redwood Manufacturing
Redwood Manufacturing, a leading producer in the automotive parts industry, was facing significant challenges with production efficiency and rising operational costs. To maintain their competitive edge and meet increasing market demand, they needed to revamp their manufacturing processes and adopt innovative solutions.
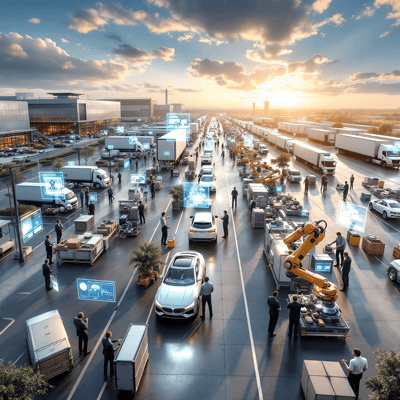
Background
Founded in 1985, Redwood Manufacturing has established itself as a trusted supplier of high-quality automotive components to major car manufacturers worldwide. With a workforce of over 1,000 employees and multiple production facilities, the company prides itself on its commitment to excellence and customer satisfaction.
However, in recent years, Redwood Manufacturing observed a decline in productivity and an increase in production bottlenecks. The existing systems and processes were no longer sufficient to handle the growing complexities of the market.
Innefficient Production Processes
- Outdated machinery leading to frequent breakdowns.
- Manual workflows causing delays and errors.
- Lack of real-time visibility into production metrics.
Rising Operational Costs
- High energy consumption due to inefficient equipment.
- Increased labor costs from overtime and manual tasks.
- Excessive material waste impacting profitability.
Quality Control Issues
- Inconsistent product quality leading to customer complaints.
- Difficulty in tracking defects and implementing corrective actions.
- Compliance challenges with industry standards and regulations.
Solutions Implemented
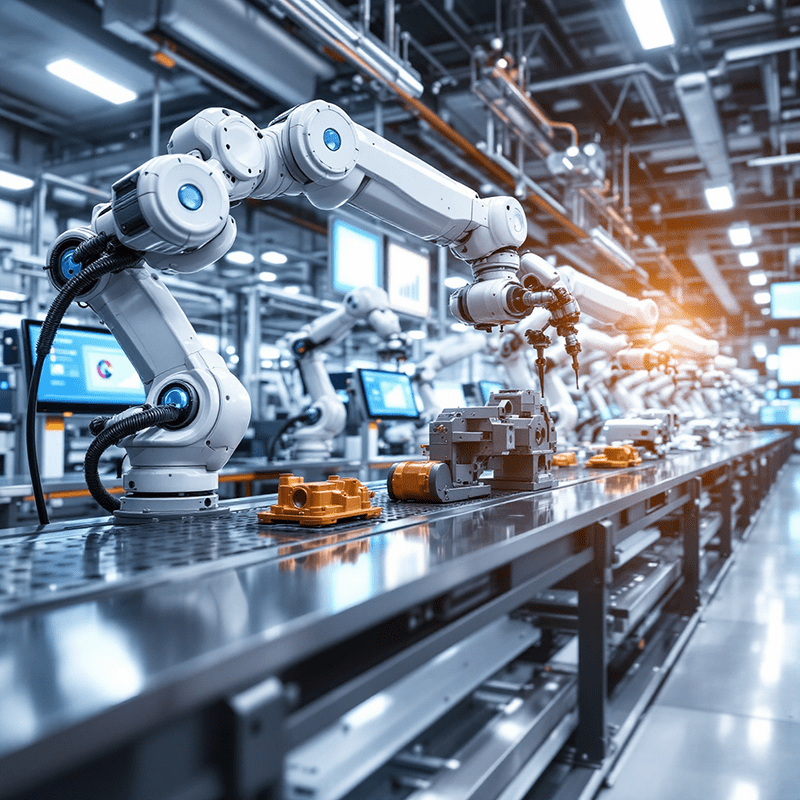
Adoption of Advanced Manufacturing Technologies
Redwood Manufacturing invested in state-of-the-art machinery and automation solutions, including:
- Robotic Process Automation (RPA): Implemented robots for repetitive tasks to enhance precision and reduce human error.
- Industrial IoT Devices: Installed sensors and connected devices to monitor equipment health and production conditions in real-time.
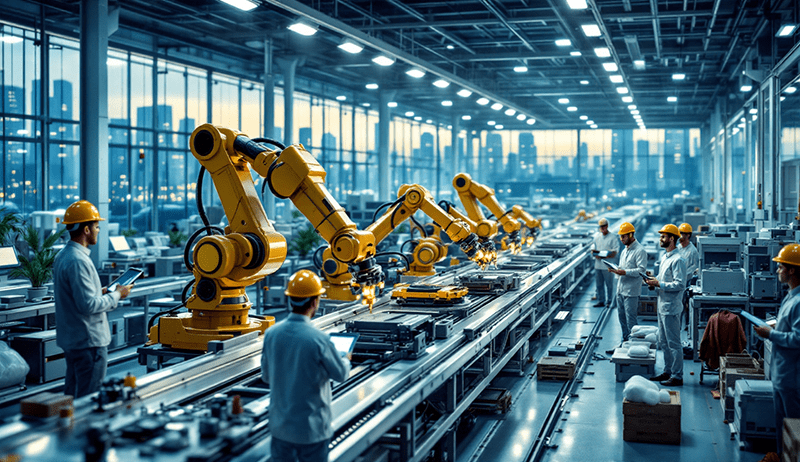
Implementation of a Manufacturing Execution System (MES)
The MES integrated all aspects of the production process, offering:
- Real-Time Production Tracking: Visibility into operations allowing for immediate adjustments.
- Data Analytics: Leveraging data for predictive maintenance and process optimization.
- Quality Management: Streamlined quality checks and compliance reporting.
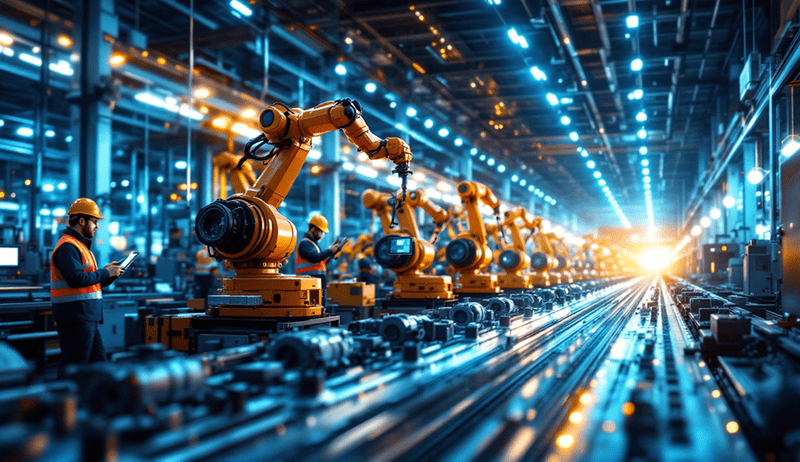
Lean Manufacturing and Continuous Improvement Initiatives
- Value Stream Mapping: Identified and eliminated non-value-adding activities.
- 5S Methodology: Organized the workplace for efficiency and effectiveness.
- Employee Training Programs: Empowered staff with skills in lean principles and new technologies.
Results Achieved
Increase in production output
Reduction in machine downtime
On-time delivery rates
Conclusion
Through strategic investments in technology and process optimization, XYZ Manufacturing transformed its operations, yielding significant improvements in efficiency, cost reduction, and product quality. This case illustrates the impact of embracing modern manufacturing solutions to stay competitive in a dynamic industry landscape.
We Innovate to Elevate Your Business
If your organization is facing similar challenges, discover how our tailored solutions can help you achieve operational excellence.
Contact Us to schedule a consultation and begin your journey toward manufacturing success.